From Here
To here:
And beyond...
The following is an example of a typical fresh engine build which can be tailored to suit individual budgetary or performance requirements.
All of our freshly built engines are stripped & dipped before the inside is coated with Glyptal.
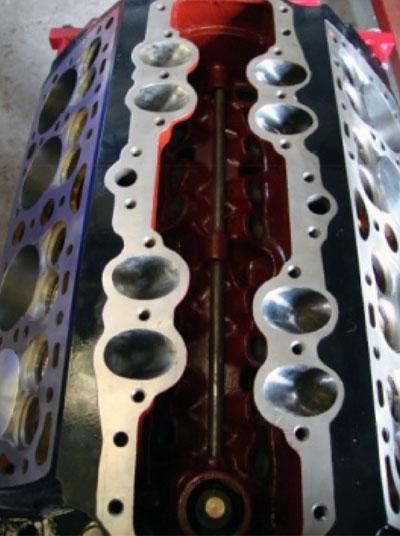
French Flathead engine blocks have the boss removed from the back of the block where clearances may be an issue (and/or to improve the look).
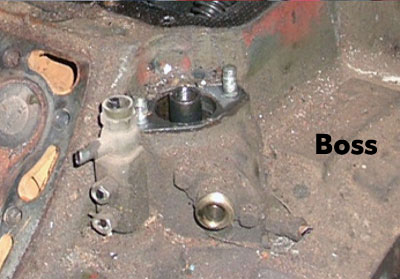
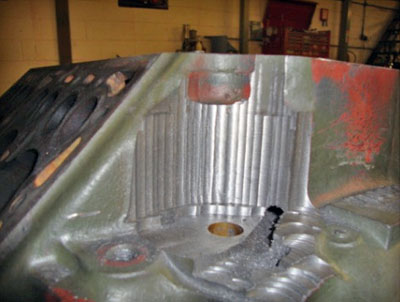
All rough casting on the outside of the block is then removed, before being etch primed & painted.
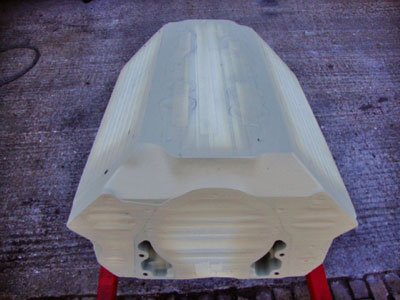
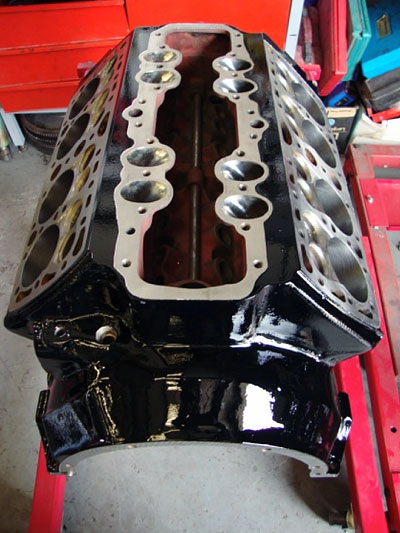
Next we move on to the dry install:
- checking all bearing clearances
- weighting valve springs individually
- complete engine balancing (pistons, rods & rotating assembly)
- lighten the flywheel
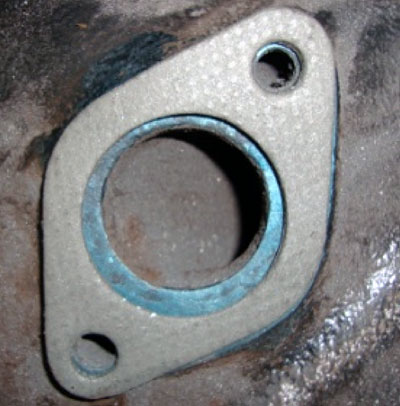
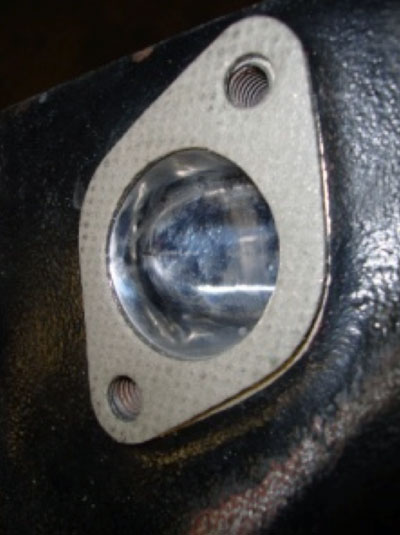
Then all machining gets done:
- custom port
- polish & relieving
- port matching
- 3 angle valve job
- 1.6 valve seats
- boring
- valley drilled
- girdle with align bore (if required)
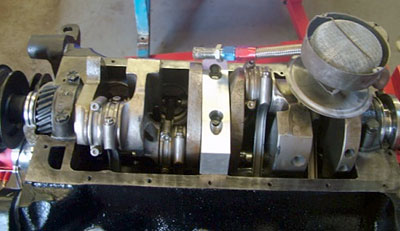
Then we strip it all down again for the final installation, in which all bearings are coated with assembly lube, & all new gaskets fitted before the engine goes onto the test stand.
Once on the test stand all engines have 5 hours running in time.
During which time engines are connected to the data acquisition computer in order to set up the carbs (re-jet) for the perfect air/fuel mixture ratio, the distributor timing & advance curve is set & heads are re-torqued.
They are run for 2 hours with running in oil, which is then drained and refilled with Miller 20/50w classic racing oil for the remaining 3 hours run time.
When customers take delivery of an engine they receive a full data sheet.
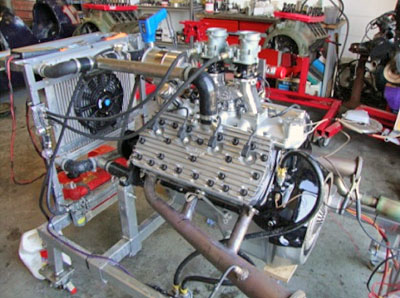